Using new analytics technologies to address process challenges and improve production makes business sense
Chemical manufacturers are continuously challenged to achieve operational excellence. Many factors are involved with reaching this goal. However, one crucial path forward is being able to fully leverage sensor-generated time-series data by being able to analyze it. Companies realize this, but without the proper tooling, they struggle to achieve this objective.
Huntsman Corp. (The Woodlands, Tex.; www.huntsman.com), a global manufacturer and marketer of differentiated and specialty chemicals, was able to overcome this challenge by empowering their process experts with self-service analytics. This tooling enabled them to answer three of the top production questions every organization like theirs is faced with:
- What is happening in the process?
- Has this happened before?
- Why is this happening?
Self-service analytics
With the self-service analytics platform supported by TrendMiner (Houston; www.trendminer.com), Huntsman process engineers and operators are able to search through historical data to look for good and bad production behavior, allowing them to carry out the analytics themselves. They can create “fingerprints” of ideal operating zones, and set monitors against these fingerprints. If a deviation occurs, alerts are sent out via messages, emails or dashboards to notify personnel about the issue, giving them time to take corrective action. A 24-hour engineering support system is therefore set in place, covering times when engineers are not on site (Figure 1). Additionally, self-service analytics can enable process experts to set monitors to predict performance and send out early warnings, and can even be used in conjunction with Lean Six Sigma continuous improvement projects.
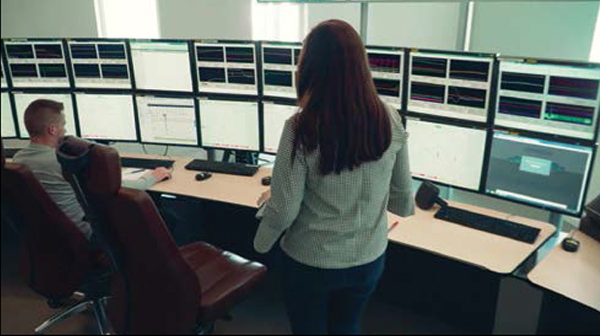
FIGURE 1. Self-service analytics monitoring capabilities provide 24-hour engineering support
Huntsman has also been able to eliminate data silos. Like many manufacturing companies, their operational data was traditionally kept in separate silos, each within its specific teams and process/business applications. With self-service analytics, users can contextualize, centralize, save and share their operational data with all teams. By eliminating these silos, it became possible to move toward combined organizational production overviews for all sites, both locally and globally. With this shared information, they saw global collaboration and team efficiency improve, which resulted in enhanced and more insightful resolution of production problems.
Fingerprinting batch processes
Traditionally, Huntsman’s teams would check batch profiles using Microsoft Excel — an approach that required a substantial amount of production expertise and time. However, after implementing a self-service analytics platform in 2018, they were able to become much more efficient by creating fingerprints of good operating zones to check batch quality against specifications.
In one of its polyols processes, distinct pressure and temperature profiles are required to consistently produce high-quality material. Huntsman’s teams used fingerprints as realtime monitors to continuously check the process for deviations. Process experts were able to quickly identify subtle disturbances that would be difficult to capture in a numerical model. As the monitors gave early warnings for unexpected heat input, there was no need to check afterward if there were any abnormalities, allowing operators to take appropriate action in time (Figure 2). This new approach to batch analysis and monitoring led to a significant reduction in off-specification batches and a significant increase in product quality.
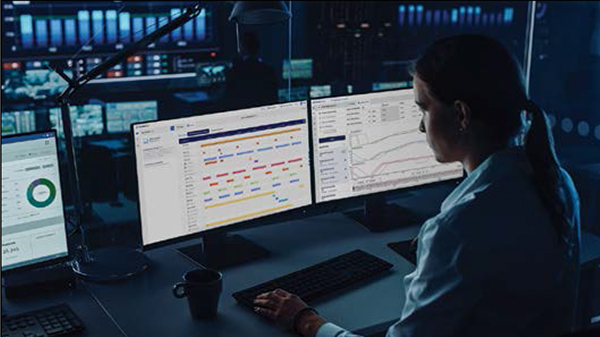
Figure 2. Setting process monitors can give process experts early warnings when batch quality is off-specification
Improving quality assurance
In one of Huntsman’s Advanced Materials plants, numerous batches in a wiped-film evaporator exceeded the solvent specification limit, resulting in off-specification products. The process experts also observed a multi-year drift in quality as measured by the quality assurance laboratory. They suspected this problem resulted from a change in testing methods, but this hypothesis and the frequency of off-specification production needed to be investigated.
A six-sigma analysis following the “define, measure, analyze, improve and control” (DMAIC) strategy was performed using the various capabilities of self-service analytics, such as value-based searches, layer comparisons, statistical comparison tables, scatterplots, filtering and the recommendation engine.
The team used scatter plots to easily track batch performances for insight about which batches were outside of the acceptable operating zone. Multiple differences between the plant’s on-specification and off-specification production campaigns were found, which convinced them that long-term changes had been occurring in the process. Further investigation allowed the process experts to rule out the misreading of flowmeters, and they found a non-negligible offset between measured and true pressure.
With self-service analytics, the process experts completed a faster root-cause analysis on a much larger data set. They were also able to identify differences in the subtle pressure readings and thus call for more tests to be conducted. Based on these findings, quality improvements were realized within days after making process changes.
Using new technology like self-service analytics can effectively address process challenges and vastly improve production. Huntsman understands this. Now, its teams of process experts have a continuous, constant view of production, resulting in more profitable and efficient production management in a highly competitive market. ■
Edited by Mary Page Bailey
Authors
Jasper Rutten (Email: [email protected]) works at Huntsman Corp. as the manager of the company’s Advanced Analytics team, which sets out the global route on digitalization and advanced analytics for upstream methylene diphenyl diisocyanate (MDI) manufacturing facilities. He joined Huntsman in 2000 after graduating as a chemical engineer from Twente University in the Netherlands. His extensive experience in chemical engineering provides a solid basis to lead the global journey of sustainably bringing industry 4.0 into practice.
Edwin van Dijk (Email: [email protected]) is the vice president of marketing at TrendMiner NV (www.trendminer.com). He has over 20 years of experience in the process and power industries. He spent more than 10 years at Greenock, selling plant design software to owner-operators and contractors, followed by a role as business development manager at BlueCielo ECM Solutions. In his last role as director of global marketing at BlueCielo, he focused on brand recognition, product positioning and go-to-market launch plans. Within TrendMiner, van Dijk is responsible for the global marketing strategy, which includes a focus on educating the market on the benefits of data analytics in the process industry and the opportunities available with TrendMiner’s solutions.