Today’s level measurement instruments are smarter, easier to use and designed to meet the challenges of the CPI
When it comes to level measurement, chemical processors long for a “silver bullet” technology that works in every application. Unfortunately, there isn’t one. On the bright side, there are many types of level measurement devices available, so one is sure to work in any given application, no matter how demanding. And that’s a good thing because in the chemical process industries (CPI), the applications tend to be both challenging and critical due to the process extremes and the materials being measured. For this reason, whatever technology is chosen, it must be both reliable in application and ensure safety, which means that today’s level measurement instruments are smarter, easier to use and designed to meet these requirements.
“Our customers want one technology that will fit all their needs and all their applications,” says Gene Henry, product marketing manager for level with Endress+Hauser (E+H; Greenwood, Ind.; www.us.endress.com). “Finding a ‘silver bullet’ technology is especially difficult in the chemical processing industries because they have higher pressures and higher temperatures, a lot of applications that are corrosive and a host of other issues, such as condensation, foam or obstructions. When you combine these characteristics and the effects they can have on instrumentation and equipment, it becomes obvious that trying to shoehorn one specific technology into all applications can’t be done.”
Selecting the right instrument for the right application can be a challenge in its own right. “Doing level correctly is an art form,” says Henry. “A device may be designed for one type of application, so it isn’t always possible to offer that same device elsewhere and know it’s going to work, but finding the right device is possible.”
To do so, processors must consider process environment factors, such as temperature and pressure, as well as conditions such as aggressive media, turbulence and condensation. Knowing the history of level measurement devices that have worked, or not, in the past is also helpful. “Often the questions come up when something isn’t working with a certain type of level instrument and we have to find the next best solution,” notes Dean Mallon, national marketing manager for level with E+H. “That’s when equipment experts have to start looking in-depth at the real parameters: the pressure, temperature, density of product, the history, how the current device has been working and what is going on that presents the opportunity to offer something else. We have to uncover the challenges and, based upon experience and knowledge, make recommendations of what might work better and then make sure the instrument is installed and configured correctly so that the new technology is bringing the reliability they expect and need.”
Difficult process conditions
Most of the difficult process conditions are related to the environment within the process, says Mike Bequette, vice president of engineering with SOR Measurement and Control (Lenexa, Kan.; www.sorinc.com). “Because every chemical and every process is different, there can be a variety of issues that present technology challenges. You can have reflections, vapor pressure, condensation, foam, agitation or turbulence in a tank, corrosive materials and the list goes on. Each of these issues can impact or affect the ability of an instrument to function reliably in any given application. For example, condensation can affect the accuracy of radar technologies or a changing specific gravity can affect accuracy of a pressure transmitter used to measure level. That’s why is it important to look at these conditions to find the right instrument for the application.”
Aggressive media. One of the biggest considerations when selecting instruments for use in the CPI is aggressive media. “In chemical processing, the materials are often toxic, aggressive and corrosive, so finding the correct instrument for those applications is important because these types of materials can affect the accuracy, reliability and safety of the instruments,” explains Herman Coello, product marketing manager for level with Siemens (Alpharetta, Ga.; www.usa.siemens.com).
Siemens introduced its Sitrans LR250 radar level transmitters with a flanged encapsulated antenna (FEA) for continuous monitoring of liquids and slurries in storage and process vessels, including corrosive or aggressive materials. The two-wire, 25-GHz pulse-radar level transmitter features a lens that is compatible with most materials and is the only part of the instrument that comes in contact with the media, says Coello. “In the past when there was a situation that involved aggressive media, we needed expensive alloys, but this flanged encapsulated antenna means corrosive or aggressive materials are no longer a challenge.”
Similarly, E+H’s Micropilot FRM62 (Figure 1) was designed for 80 GHz level measurement in aggressive liquids. The radar technology offers a completely PTFE-filled (polytetrafluoroethylene) and flush-mounted antenna. The integrated PEEK (polyether ether ketone) antenna allows very small process connections and the free space radar provides reliability due to improved algorithms and small beam angle.
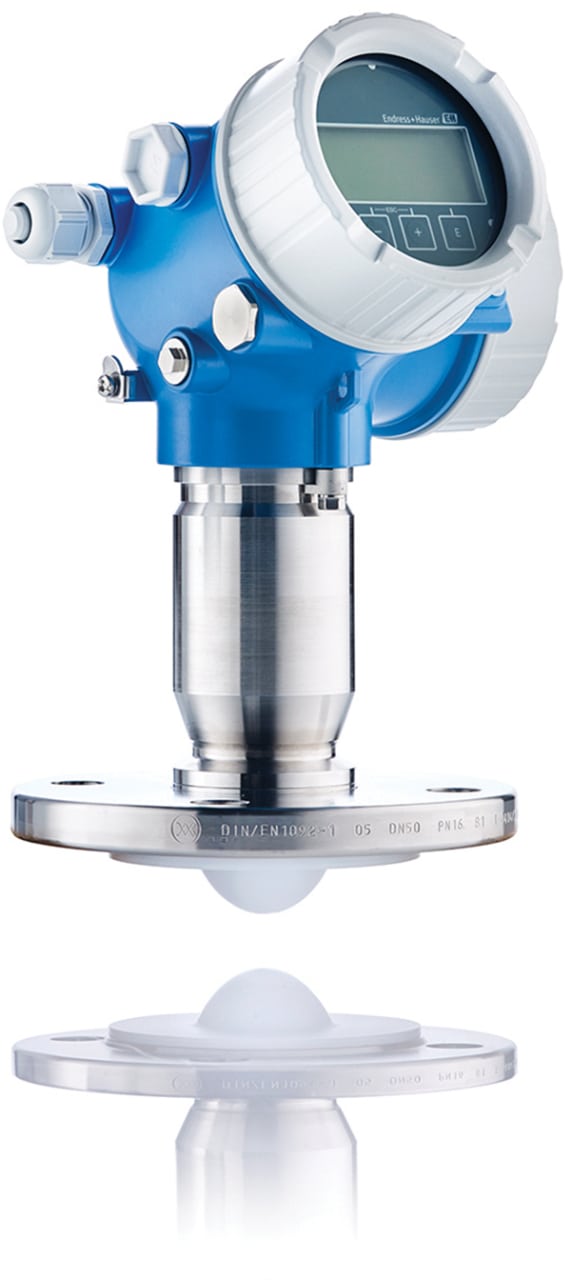
Figure 1. Endress+Hauser’s Micropilot FRM62 was designed for 80-GHz level measurement in aggressive liquids. The radar technology offers a completely PTFE-filled and flush-mounted antenna
Endress+Hauser
Another benefit of this technology is that it provides an advantage in the chemical industry where many of the vessels are tall and narrow with a lot of obstructions, notes E+H’s Mallon. “The small beam angle of the instrument and our Multi-Echo Tracking evaluation provide the ability to measure reliably in these types of vessels, even in aggressive liquids,” notes Mallon.
Vessel size and obstructions. Ingemar Serneby, senior applications specialist for measurement and analytical with Emerson’s Rosemount Level Center of Excellence (Gothenberg, Sweden; www.emerson.com), agrees that the vessels used in chemical processing can also pose a challenge. “They can be quite small in size and contain heating coils, agitators and baffles, which reduce the surface tension and cause turbulence, foam and other factors that can be challenging,” he says. “For these situations, we recommend non-contacting radar with frequency modulated continuous wave (FMCW) technology,” he says. “FMCW is more sensitive than previous technologies so it allows measurement despite things like obstructions, turbulence and foam.”
Emerson offers its Rosemount 5408 non-contacting radar level transmitter (Figure 2) for both liquid and solid materials measurement. Using two-wire FMCW technology, the instrument deploys a continuous echo to maximize radar signal strength and produce a reliable measurement in demanding applications.
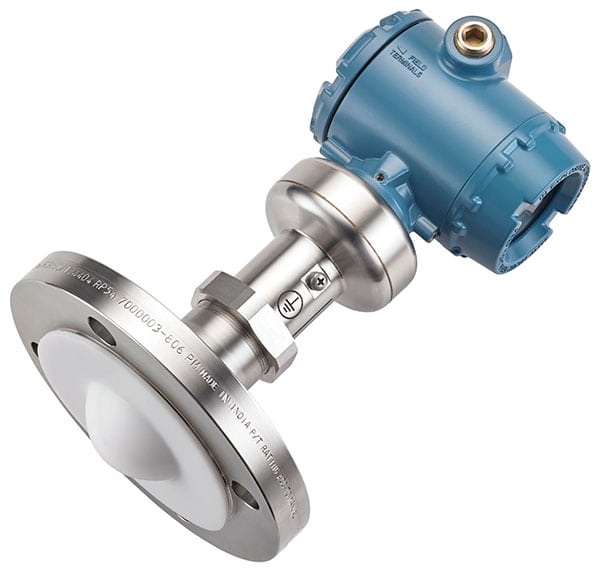
Figure 2. The Rosemount 5408 non-contacting radar level transmitter uses two-wire FMCW technology and deploys a continuous echo to maximize radar signal strength and produce a reliable measurement in demanding applications
Emerson
When it comes to small tanks, perhaps no other vessels are more challenged than those used in R&D applications, which employ scaled-down versions of larger process equipment, but still face the same process challenges, such as pressures, temperatures, corrosive media and other process issues, including foam and condensation, says Steve Sawyer, technical sales manager with Dynatrol (Houston; www.dynatrolusa.com).
“Imagine a scaled-down version of a hydrocarbon cracking application,” he explains. “Rather than a 100-ft cracker, you’ve got a 3-ft vessel with high temperatures and high pressures, so you need a reliable level measurement device that will work within these scaled-down parameters,” he says. His company offers the Dynatrol CL-10H liquid level switch, which has no packing gland, diaphragm, float, bearing, bellows or pressure seal in its design. The device provides rugged construction with a sensitive transmission of vibration energy through a rigid, all-welded pressure seal. “It’s a unique device in that it works on a vibration principle, which provides an accurate level measurement within a high-pressure, high-temperature vessel and provides an output signal that can feed into the program that is controlling the other functions of the process,” says Sawyer.
Steam generation. Another common challenge in chemical and petrochemical processes, says Emerson’s Serneby, is that they sometimes generate a lot of steam, which can also affect level measurement. “It is difficult to handle steam with traditional devices,” he says. “So for our guided-wave radar, we have developed dynamic vapor compensation technology that measures a reference and compensates for the propagation of the wave in the vapor space.” The Rosemount 5300 Series guided-wave radar transmitters with this option eliminate accuracy errors associated with varying pressure and/or temperature that occur in vessels involving steam vapor. The dynamic vapor compensation option includes a probe with a built-in reflector and software, offers safety with a gastight dual seal, is corrosion-resistant and has no moving parts. It uses a reference reflector at fixed distance on a rigid single probe to measure vapor dielectric.
Wet solids. Another tough application involves the measurement of solid materials where moisture may be present, says Jack Evans, president of Hawk Measurement (Lawrence, Mass.; www.hawkmeasure.com). “When it comes to the measurement of solids, it must be emphasized that there are industries that have dry solids, and then applications that have moisture,” he says. “And in these level measurement applications, things must be kept clean so that performance can continue, so there either has to be lots of periodic maintenance to keep the sensing elements clear of coating or the technology must have that feature built in. Hereto the technology of acoustic wave, which has the built-in capability to keep the propagating sensor surface free of coating or buildup, regardless of the material being wet or dry” (Figure 3).
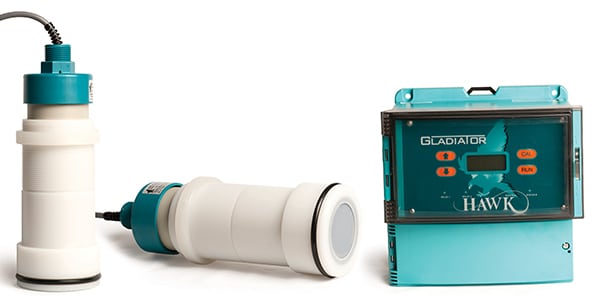
Figure 3. Acoustic wave technology, such as the Gladiator Acoustic Switch from Hawk Measurement, provides better performance in tough solids applications with heavy, wet buildup and moisture in the environment
Hawk Measurement
While acoustic wave has sometimes been considered to be the same as ultrasonic technology, Evans suggests that acoustic wave provides better performance in tough solids applications with heavy, wet buildup and moisture in the environment. He says the technology is not affected by the coating or buildup because its low frequency and high power create strong frequent pressure-wave activity on the transducer face, which keeps the material off. This pulsing power on the transducer provides the self-cleaning feature that provides the better performance under these demanding conditions.
Safety requirements
While not a process challenge, per se, more chemical processors are demanding safety certified level instruments due to the hazardous nature of the materials and the criticality of the processes. “We are seeing more significant trends toward increased regulatory control and more awareness of safety in the industry, along with a need for greater reliability in spill prevention and overfill protection applications,” says Bob Irving, director of marketing and business development with Ametek Drexelbrook (Horsham, Pa.; www.drexelbrook.com). “So our focus has been on adding safety certifications and developing instruments that help eliminate any possibility of a spill condition.”
As such, the company expanded its point level offering with a fully certified SIL 2 (safety integrity level 2) safety point level switch that provides highly reliable overfill protection, specifically for applications in which there is a high cost of failure. The Drexelbrook Safety IntelliPoint RF represents a significant advance in RF admittance reliability that addresses applications requiring safety instrumented functionality (Figure 4). The SIL IntelliPoint offers a full line of measurement probes to fit any process application where safety overfill protection is required. The premium point level switch was designed to perform in challenging operating environments with extreme reliability while meeting API 2350 overfill protection standards. Its features and functions also make it suitable for use in safety-related systems with requirements for functional safety for SIL 2 (SIL 3 with redundant switch). It is certified in accordance with IEC61508-2 and has worldwide hazardous area approvals.
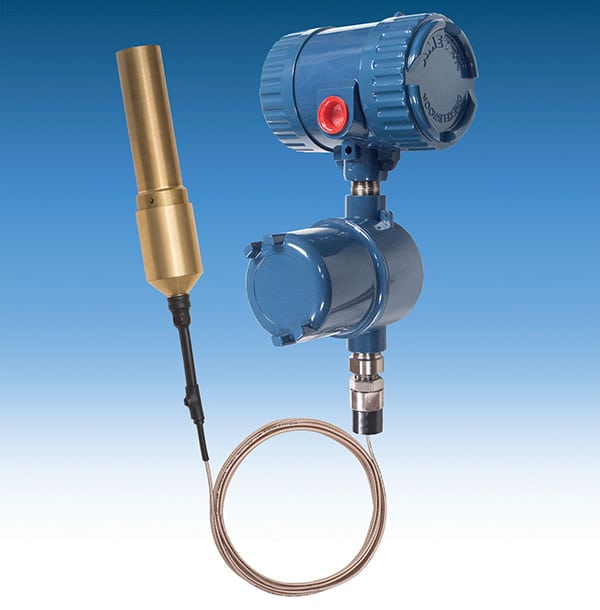
Figure 4. The Drexelbrook Safety IntelliPoint RF represents a significant advance in RF admittance reliability that addresses applications requiring safety instrumented functionality
Ametek Drexelbrook
Intelligent instrumentation
Because level measurement is often used in critical applications, chemical processors began requesting smarter instruments that could alert them when there was a problem, so many equipment providers have added diagnostic functionality to their level-measurement devices.
“We’ve spent a lot of time adding intelligence to our instruments in an effort to help customers know when something is happening with the instruments before it leads to failure of the instrument,” says E+H’s Henry. E+H’s Mallon continues, “We call it HeartBeat technology, and it can monitor how the instrument performs today compared to how it performed when it was new. The instrument can take those values, monitor the quality of the signal and transmit the data so that the users can use it to do predictive maintenance and respond to issues before failure happens, before they lose quality of the product, before they have a spill or before they have a safety issue.”
In addition to diagnostic abilities that improve reliability, the built-in intelligence gives processors information they can use to improve the process throughput and efficiency, says SOR’s Bequette. “If the device can provide information on level, temperature and other parameters across the vessel, it provides the end user with more data to make better decisions about how to run the process or the reaction to get better throughput.”
In an effort to provide more information on the instrument and process, SOR introduced its 815 DT smart differential pressure transmitter (Figure 5), which can be used for level, differential pressure or flow measurement in hazardous locations and hostile environments, and is available with a low-power option that allows it to operate with wireless systems. “It is a highly advanced instrument that provides all the necessary information on several parameters, as well as level and volume out of tank, and can measure and produce a discreet output for control of things like turning on a pump or opening a valve.”
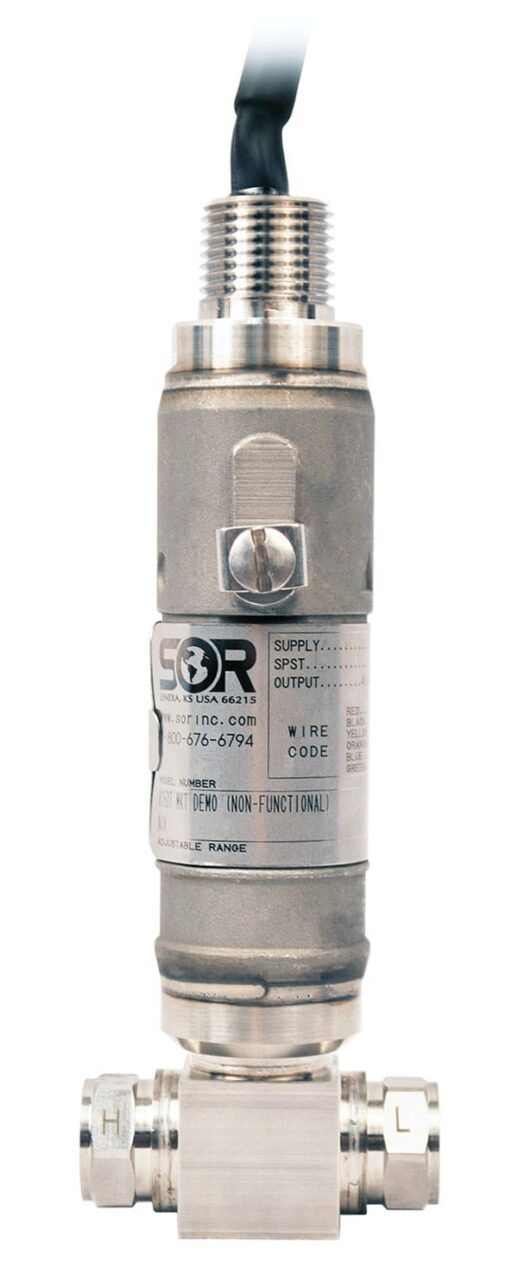
Figure 5. SOR’s 815 DT smart differential pressure transmitter can be used for level, differential pressure or flow measurement in hazardous locations and hostile environments, and is available with a low-power option that allows it to operate with wireless systems SOR
While there appears to be a dizzying array of level technologies available with different advantages, features and levels of intelligence, every technology does have its place somewhere in the process industry. “Whether it is liquid or solid material, the selection of the technology must be reviewed carefully and all applications of dust, condensation, surface conditions, temperature and pressure and many more have to be considered,” explains Hawk’s Evans. “One technology should not be considered the universal solution to all level measurement applications, as there are likely other technologies that will fit more appropriately in an application.”