Three of the critical aspects of dust collection systems are properly identifying necessary dust capture points, effectively capturing dust at each point and accounting for solids loading in the ductwork. Key considerations for these aspects are presented here
Dust collection technology is used in nearly all manufacturing industries to reduce and capture fugitive dust. This is done for a variety of reasons, including to minimize respirable dust, to minimize the “fuel” for combustible-dust hazards, to meet environmental and workplace safety regulations, to remove unwanted fines and dust from a product stream, or otherwise just “keeping a clean house.” Dust collection to reduce fugitive dust emissions is often used as an engineering control method to not only minimize dusts for the purposes stated above, but also to prevent dusts from one area of a process or facility from being transported to other areas or process equipment.
Although dust collection has been used since the 1800s, and is even more prevalent throughout industry today, dust collection systems often operate poorly because of improper design that does not properly account for the solids and their specific properties.
There are several important considerations associated with the design of dust-collection systems that require attention in order to ensure that the system successfully mitigates excessive dust releases and operates reliably without plugging. They are listed below:
1. To effectively capture dust at each collection point, identify not just the process’ major fugitive-dust generation points, but the points where dust capture and collection is actually required.
2. When designing the dust-collection system, take into account the solids/dust loading in the ductwork.
3. Ensure reliable transport of the collected dust through the ductwork.
4. Ensure proper airflow balancing across the system.
5. Avoid plugging in both the ductwork and the filter.
6. Ensure the filter/collector is adequately designed to filter the dust from the air.
7. Ensure the air mover for the system (typically a fan) is adequately designed and sized for the application.
8. Consider dust hazards, including combustible-dust hazards, toxicological hazards and environmental hazards.
This article focuses on the first three of the above considerations, and discusses some common design mistakes. These include having unnecessary pickup points where dust capture and collection is not actually needed, failing to account for the solids loading in the design of the ductwork, and poor dust capture at each point where collection is required (often due to the hood being too far from the dust-generation point).
Dust generation and capture points
All dust collection systems, regardless of size and number of pickups, are dedicated systems that use vacuum pressure (suction) to capture dust from one or more localized points and accumulate the dust in another separate area. Dust collection systems all have four key components, illustrated in Figure 1: one or more dust capture hoods/pickup points, the ductwork/piping, the solids disengagement/air cleaning device (the filter receiver or collector, often a baghouse) at the end of the ductwork, and the air mover (often a fan in dust-collection applications). All components need to work effectively and in concert for the dust collection system to perform successfully as designed. Unfortunately, dust collection systems don’t always work as desired, and they can often wind up as a key bottleneck in a process.
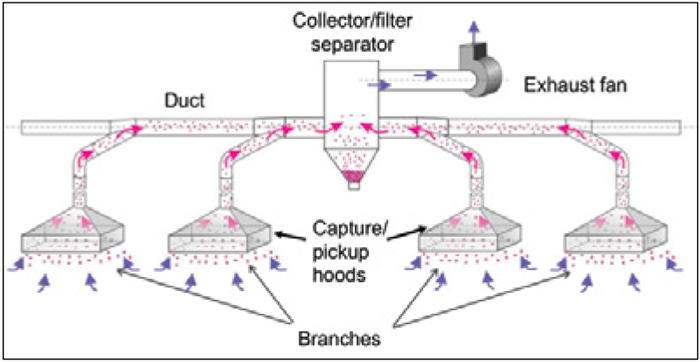
FIGURE 1. The diagram shows the components of a typical dust-collection sytem, including pickup points and ducting [1]
Dust collection systems range in size, from large fixed and centralized systems that can have dozens of pickups (dust capture points) across several process areas, to smaller fixed systems with only a few dust pickups localized to specific processes or equipment, or mobile systems for “as required” point-of-use dust capture.
Fugitive dust may be generated or released in a variety of different industrial operations, as follows:
• Operations that tend to generate the most dust are those where there is high-energy, forceful mechanical breakdown of a material. Examples of this include comminution/particle-size-reduction equipment, such as crushing or milling, as well as grinding, sawing, sanding or polishing equipment.
• Operations that may release some dust include those where there may be leakage from equipment, for example, through shaft end seals of rotating equipment or leaky gaskets.
• Operations that tend to generate less dust include those where there is displaced air and entrainment of fine particles into air due to shaking, free-fall, or aeration, where particles can unintentionally break apart and generate more fines. Examples of this include screening, filling and discharge of bins, silos and hoppers, as well as bag filling or dumping, mixing and blending operations, pneumatic or mechanical conveyance, impacts in transfer chutes and at the receiving conveyor, transfers between conveyors or other equipment, and so on.
Dust-collection pickups should generally be located nearby these dust-generating operations whenever dust capture and collection are required. However, one important (but often overlooked) point is that not all dust generation points require dust collection. In fact, there may be situations where dust capture and collection for a given operation could be avoided, and others where dust collection is absolutely required for one reason or another. To determine whether dust capture and collection is actually required at a dust-generation point, consider the following questions:
a. Would even minor fugitive dust releases or leaks potentially create a highly hazardous condition (for example, if the dust itself has significant combustibility or toxicity hazards, or if the presence of the dust in the surrounding area would create a hazard)? Or alternatively, would it be sufficient to mitigate the hazard from fugitive dust using routine housekeeping activities?
b. Is it impossible or impractical to design and maintain the equipment to prevent or minimize dust generation in the first place?
c. If dust generation cannot be prevented and the equipment is not likely to become pressurized, would it be impossible or impractical to design the equipment to keep the dust contained locally?
d. If dust generation cannot be prevented and the equipment may become pressurized, would it be impossible or impractical to keep the dust contained within the equipment using local ventilation (with passive or active vent filters) rather than connecting to a dedicated dust-collection system to remove the dust to another location?
If the answer to the questions above is “no”, then the best approach would generally be to not capture and collect the dust at that generation point.
As an example of unnecessary dust collection that illustrates some of the problems it can create, enclosed equipment (such as silos or enclosed conveyors) is often designed with dust collection pickups connected to a dedicated dust-collection system. These pickups were often installed to avoid dust leaks by providing some suction (negative pressure) on the equipment and preventing it from becoming pressurized when air is displaced as the equipment is filled with material. The negative pressure may also be in place simply because the equipment has leaky gaskets or covers. These pickups often create significant problems — the ductwork in those particular branches often becomes plugged due to poor duct layout and insufficient velocity (after all, where is the airflow in the branch coming from if the pickup is connected to enclosed equipment?). These duct branches regularly cause issues for the rest of the dust collection system as well.
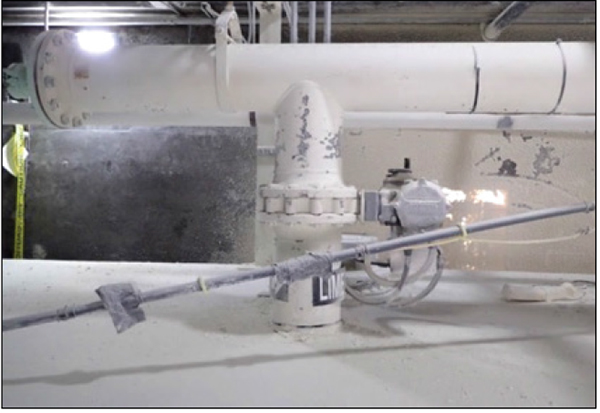
FIGURE 2. The photo shows a dust-collection pickup on an enclosed silo headspace
Figures 2 and 3 show an application that illustrates this, where several silos were filled pneumatically with material by bulk trucks, and pickups for a central dust-collection system had been installed on the silo headspace to try to prevent the silos from becoming pressurized and prevent dust clouds from being released through the pressure-relief valve. The dust collection system plugged extremely frequently (both in the ductwork and at the collector), creating a critical bottleneck in the process that required maintenance shutdowns for cleanout after every single truck unload. These plugging problems not only required operator intervention to resolve, but also made it so that large dust clouds were regularly released from the silo relief valves despite the dust-collection system, since the silos were still becoming pressurized.
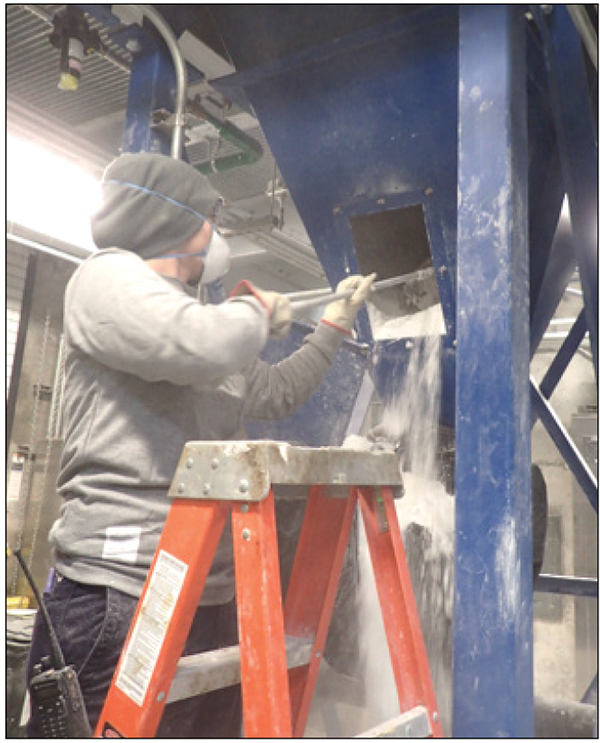
FIGURE 3. An operator deals with plugging in a dust-collector hopper
The problems were resolved and the process bottleneck removed by keeping the dust contained within the silos, thereby eliminating the need for central dust collection entirely — local vent filters with cartridge filters were installed on the headspace of each silo, with small fans to provide slight active suction to avoid pressurization of the silo headspace during filling.
Consider solids loading
Dust collection systems are often designed based on standard HVAC (heating, ventilation and air conditioning) system principles, calculations and design procedures, such as those given in Refs. 2 and 3. These references also provide some helpful guidance on typical ranges of duct velocities and dust-capture velocities that may be used for various applications. The actual design parameters required to ensure the performance of a given dust-collection system will obviously depend on the specific application, operations and material properties.
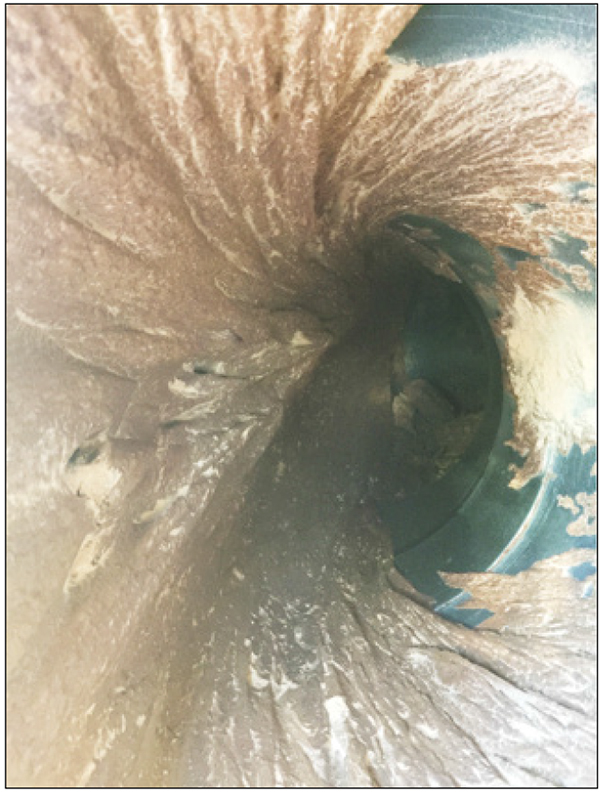
FIGURE 4. Buildup of sticky dust in a 30-in. diameter duct is shown here
Unfortunately, these HVAC-system design guides are for ventilation with air only, and do not account for dust loading in the ductwork. HVAC system design calculations for determining velocities and line resistances (static pressure; SP) may be essentially valid in systems with extremely lean dust loading. However, dust can frequently build up and plug in the ductwork in many applications, even if the velocities are nominally high enough to capture the dust and transport it through the ductwork, if the solids loading is not properly considered during design. Duct plugging occurs particularly often with moist, cohesive or sticky dusts (Figure 4), or if there is (or may be) condensation in the duct. Plugging also occurs if the duct velocity is no longer high enough due to increased system SP or the ductwork is poorly laid-out and saltation occurs (Figure 5).

FIGURE 5. When solids loading is not taken into account in duct-system design, saltation and buildup can occur
If dust saltation or buildup does start to occur, it often tends to lead to a chain reaction that ends in plugging — the saltation or buildup reduces the effective duct diameter, increasing line resistance and system SP, which in turn reduces the airflow the fan can provide (potentially by 30% or more), causing the duct velocity to decrease, likely leading to more saltation and buildup, and eventually leading to duct plugging.
Furthermore, it is often important for the dust-collection-system design calculations to account for the solids loading in the ductwork, and include additional line resistance required to accelerate and transport solids through the system. If these additional losses, or resistances, from solids loading are overlooked in the system design calculations, or if the dust loading in the system is higher than anticipated (for example, due to excessive dust generation or overly-aggressive dust capture at one or more capture points, or due to heavy dust particles), there may be significant problems with the system. As an example, if some of the capture points have much higher dust generation than others, and the increased dust loading in those branches is not properly accounted for in design calculations, the additional resistances due to higher dust loading in those branches may lead to the system’s airflows being unbalanced. The additional SP from solids loading may also make it so that the fan is significantly under-designed and unable to provide the necessary airflows and velocities required for adequate dust capture and avoiding plugging in the ductwork.
Capture the dust at each point
The system may not be capturing enough dust at each generation point if there is not adequate airflow to ensure sufficient velocity at the dust-generation point, which depends not just on the fan and system design, but also on the actual design of the capture hood/pickup point and its location relative to the dust-generation point. There are a variety of different dust-capture hood design configurations available, depending on the needs of the application. Different hood designs have different relationships between the velocity at the capture hood face (Vface) and the actual capture velocity at the dust-generation point (Vc,act).
As a simple example, if an unflanged, round plain-end pipe is used as a dust pickup, the relationship between Vface and Vc,act follows the DallaValle equation:
(Vc,act /Vface) = Ad/(10x2 + Ad)
where Ad is the area of the pipe face, and x is the distance of the hood face away from the dust-generation point [1].
Therefore, if an 8-in.-dia. (Ad = 50 in.2) pickup is located only x = 4 in. away from the dust-generation point, the actual velocity at the dust-generation point (Vc,act) is only about 24% of the velocity at the hood face Vface. At x = 8 in. away, Vc,act is only 7% of Vface, and at x = 12 in., Vc,act drops to only 3% of Vface. This means that if the dust-capture hood is located even a seemingly small distance away from the dust-generation point, it loses a significant amount of its ability to capture and collect the dust. As a result, it is critical to locate the capture hood close to the dust-generation point to avoid the rapid loss of air velocity as a function of distance from the hood face, and to factor up the airflow at the hood as required based on velocity loss at distance x. Figure 6 shows an example of a capture hood located too far away from a dust-generation point, leading to significant dust release from even a short free-fall with a fine powder. The dust capture point in Figure 6 is also completely open to the surrounding atmosphere. There should be walls to better enclose the dust-generation point to direct the airflow through the dust cloud and improve the effectiveness of dust capture.
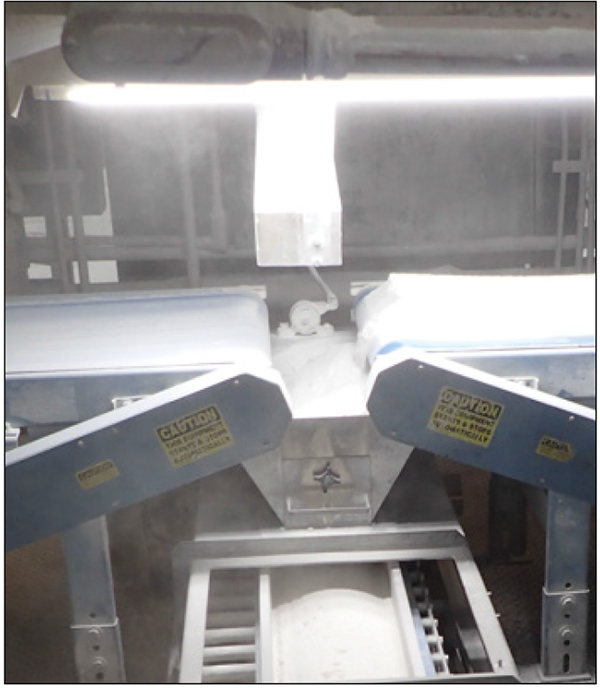
FIGURE 6. This photo shows an example of a dustcapture hood that is located too far from the dustgeneration point
It is also possible that the actual SP for specific duct branches and for the overall system may be higher compared to the design value, potentially due to buildup in the ductwork or to closed (or partially closed) blast gates. The higher SP can also occur if the solids loading in the system was not properly accounted for. Higher SP versus design may be reducing the overall airflow in the system due to limitations of the fan, and potentially throwing off the system SP balancing. This may reduce the airflow and capture velocity in specific branches, and therefore decrease the amount of dust captured at different pickup points.
It is important to not only capture enough dust, but also to avoid capturing too much dust — improperly-designed dust collection systems can often pull excessive material into the ductwork, including “good” product, along with fugitive dust. Not only may this be lost product (and therefore lost revenue), but it also increases the dust loading and resistance/SP in the ductwork, potentially leading to some of the problems discussed previously.
To minimize the risk of bottlenecks due to poor dust-collection system operation, it is critical to consider both your specific application and your material’s properties, as measured by proven test methods [4].
Edited by Scott Jenkins
Acknowledgements
Figure 1 is reprinted with permission from Ref. 1. All other photos are courtesy of Jenike & Johanson
References
1. Cecala, A.B. et al., National Institute for Occupational Safety and Health (NIOSH), “Dust Control Handbook for Industrial Minerals Mining and Processing, 2nd ed.,” 2019, NIOSH publication no. 2019-124, RI-9701.
2. American Conference of Governmental Industrial Hygienists (ACGIH), “Industrial Ventilation Manual,” 23rd ed., 1998.
3. Burgess, W.A., Ellenbecker, M.J., and Treitman, R.D., “Ventilation for Control of the Work Environment, 2nd ed.,” Wiley-Interscience, 2004.
4. J. Marion, “Bulk Solids Flow: Know What You’re Dealing With”, The Chemical Engineer, June 2020, no. 948, pp. 36–40.
Author
Josh Marion is a senior project engineer with the bulk-solids and powder-handling equipment engineering firm Jenike & Johanson, Inc. (400 Business Park Dr., Tyngsboro, MA 01879; Phone: +01-978-649-3300; Email: [email protected]). In his 10 years at Jenike, Marion has worked on hundreds of projects across all major manufacturing industries for designing new bulk-solids handling systems and developing customized retrofit modifications for existing installations to ensure reliable material flow and transport, including dust collection systems. Marion holds both B.S. and M.S. degrees in chemical engineering from Northeastern University in Boston.